Interactive Fabrication
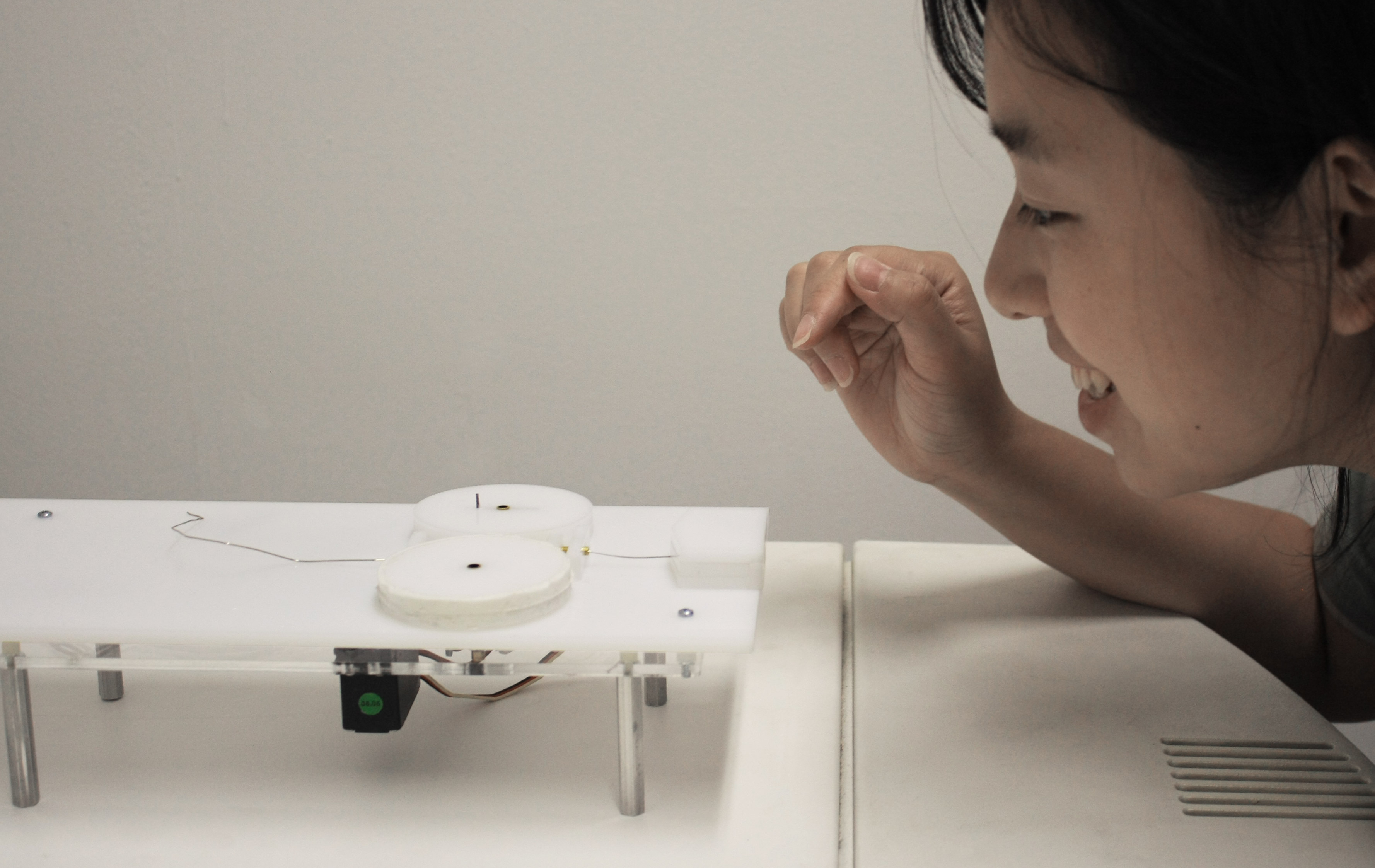
Interactive Fabrication is a series of prototype systems that map out the problem space of new interfaces for digital fabrication. Although conventional graphical user interfaces (GUI) coupled with digital fabrication allow for precise control, they are far removed from traditional craft where the designer interacts directly with material using hand tools. Interactive Fabrication explores when alternate interfaces are useful and what direct manipulation can enable.
Created by: Karl D.D. Willis, Cheng Xu, Kuan-Ju Wu, Golan Levin, & Mark D Gross
Research Paper: Interactive Fabrication: New Interfaces for Digital Fabrication
Funded By: Fine Foundation Grant
Selected Press: BBC, New Scientist, Wired, Fast Company, Creative Applications, Gizmodo, Engadget, Design Boom, Wired, New Scientist, Joystiq
Speaker
Speaker interactively sculpts wire forms based on sound input. The user stands in front of the device and speaks into a small microphone. The device then begins to push and bend the wire into a simplified sound wave contour based on his/her utterance. Sounds are thus physically 'encoded' into the wire, creating a tangible manifestation of an intangible sound.
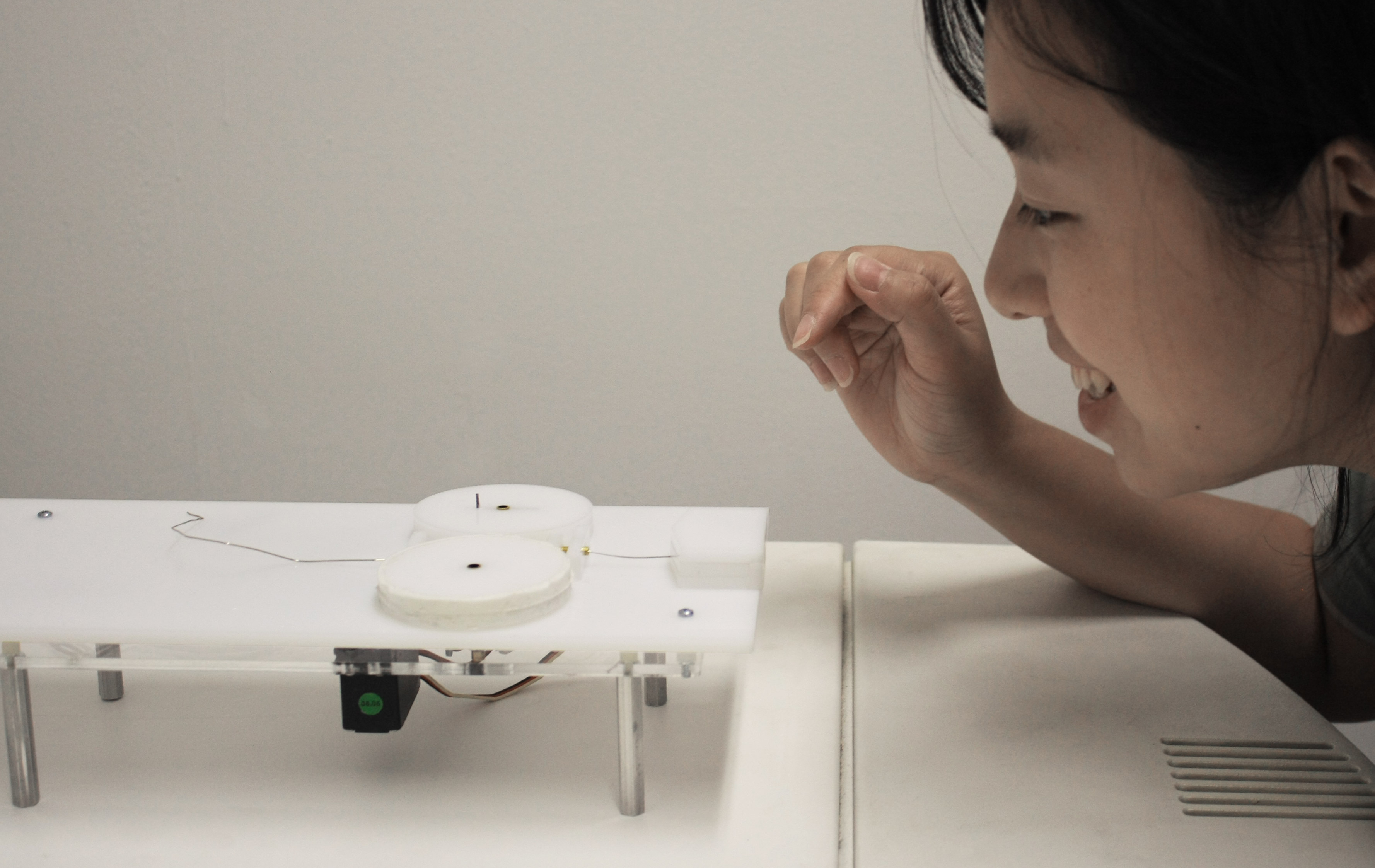
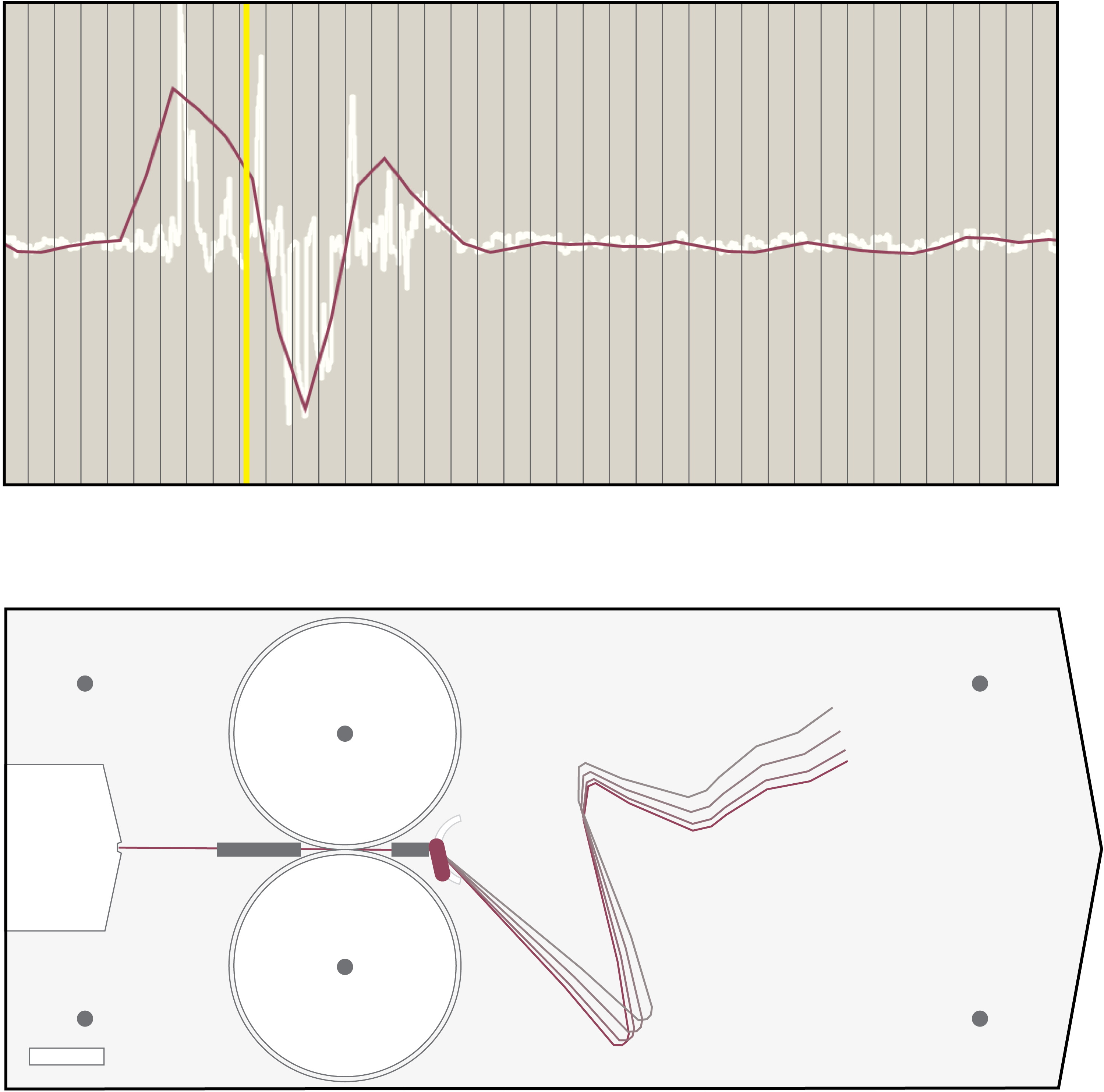
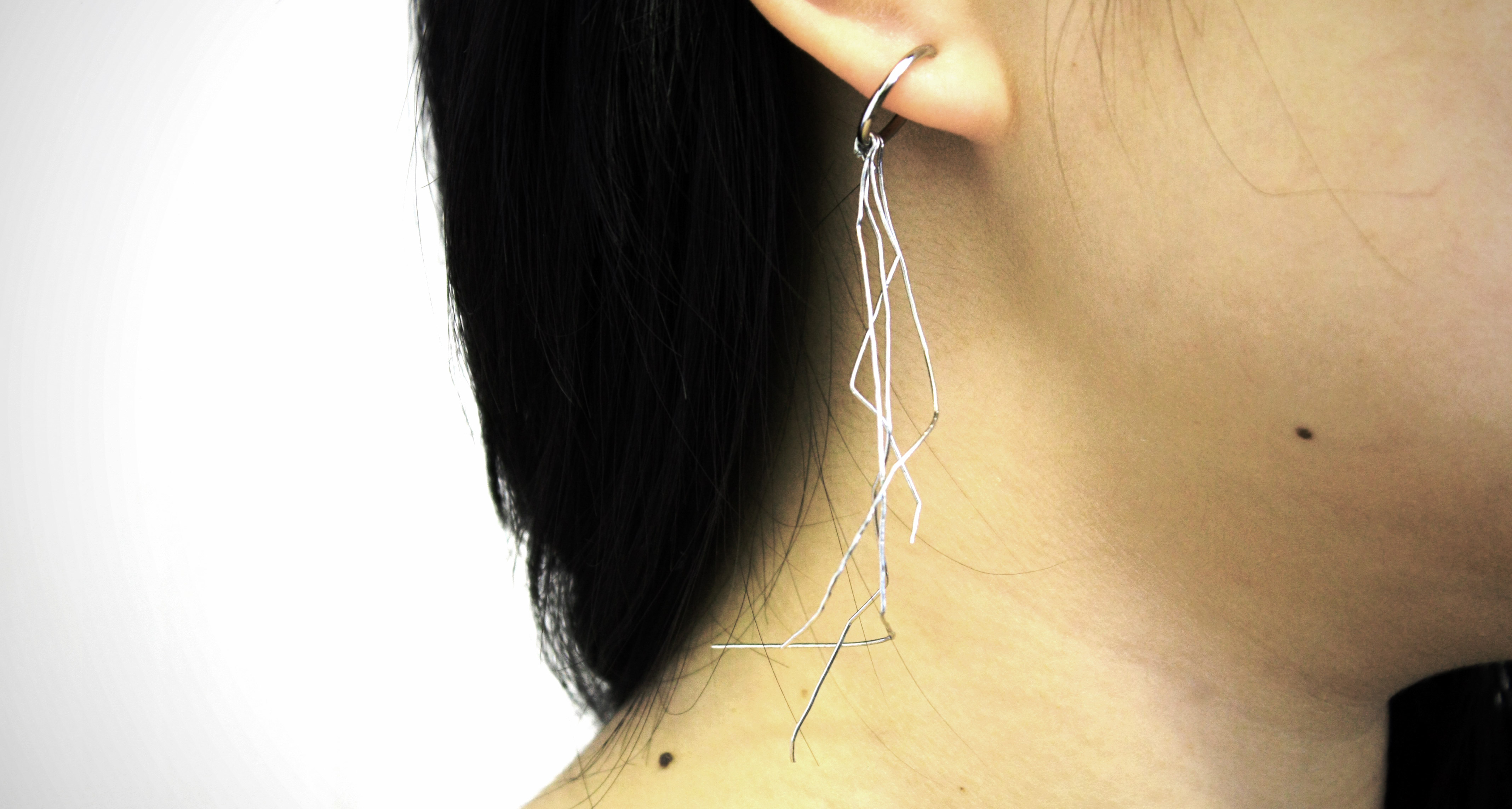
Cutter
Cutter is a tangible interface for generating three-dimensional digital models by hand crafting polystyrene foam. The user pulls, pushes, and rotates a custom hotwire cutter to sculpt, cut, and shape foam cubes. The position of the cutting path is processed in real-time by a computer to visualize the cutting process and generate a 3D model. Cutter aims to provide an intuitive way to explore physical form by combining traditional craft with digital fabrication.
Shaper
Shaper is a prototype device that uses a three-axis computer numerical control (CNC) machine to interactively dispense expanding polyurethane foam material. The user controls the device via a translucent touch screen to create physical artifacts with sketch-like gestures. Shaper challenges the conventional process of digital fabrication by allowing direct interactive control.
Beautiful Modeler
Beautiful Modeler is a software tool for gestural sculpting using a multi-touch controller such as an iPad. Each finger is used to control a single touch point in the model, with multiple layers working to build up 3D volume. As the controller is connected over the wireless network, it can be moved freely to change the viewing angle of the model. The finished mesh can be exported as an STL file, meaning the sculpted form can be fabricated immediately. In the example below the positive mesh has been post-processed to create a negative form for fabrication with a plaster-based 3D printer. A simple circuit is then affixed inside the form to create a lamp.
Trace Modeler
Trace Modeler is an application that uses real-time video to create three-dimensional geometry. The silhouette of a foreground object in a video frame is subtracted from the background and used as a two-dimensional slice. At user-defined intervals new slices are captured and displaced along the depth axis. The result is a three-dimensional model defined by silhouette slices over time. Geometry can be exported as a generic STL mesh file, opening up a number of possibilities for working with the mesh in more conventional modeling software. Alternatively the mesh can be used as-is for immediate fabrication using a 3D printer.
Fabricate Yourself
Fabricate Yourself is a project that documented the Tangible, Embedded and Embodied Interaction Conference. Usually we think of documentation in terms of text, photography and video, but given the tangible theme of the conference we decided to engage the community by capturing and fabricating small 3D models of attendees. This enabled us to build a tangible model of the event and fabricate it piece by piece during the conference.
Attendees firstly capture their favorite pose using a Microsoft Kinect. The depth image from the Kinect is processed into a mesh and displayed onscreen in real-time. At any time they can capture the mesh and save it as an STL file. Dovetail joints are automatically added to the side of the models so they can be snapped together. This allows multiple models to be connected to form a larger overall model.